
Siemens Rastatt tackles scalability challenges of visual inspection systems by using EthonAI’s Inspector software.
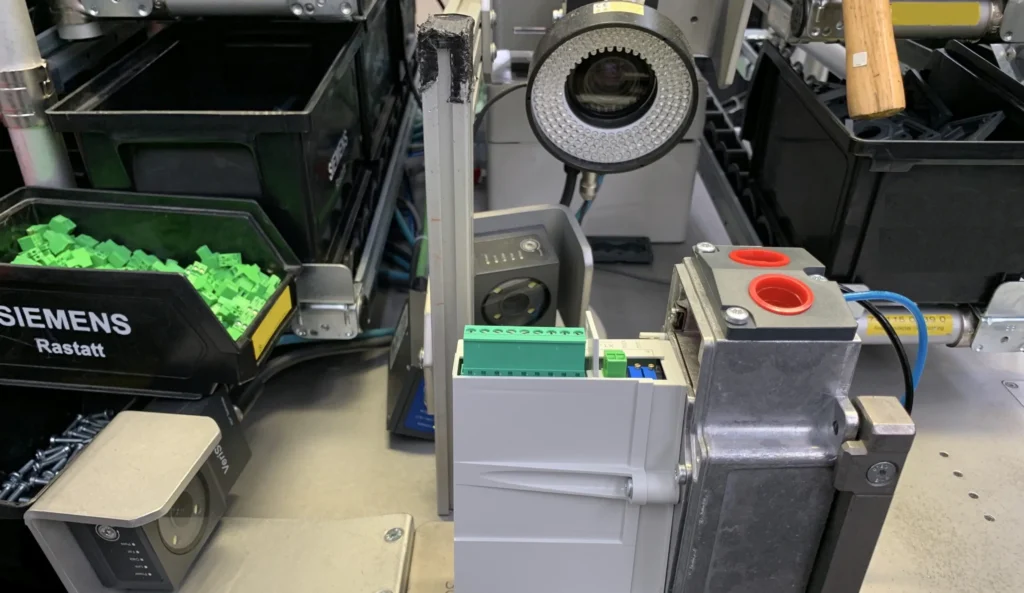
Industry
Electronics
Location
Germany
Product
Inspector
Siemens Rastatt, well-known for its highly automated facility, boasts a continually growing product variety. As a part of Siemens Building Products, the Rastatt site specializes in producing components for heating, ventilation, and air conditioning systems, which are commonly found in residential and commercial spaces. Many of these products are safety-critical, meaning that impeccable quality standards are a core priority for Siemens Rastatt, therefore placing high demands on their visual inspection systems – high demands that must be met.
The ever-growing product variety at Siemens Rastatt made it difficult to scale conventional visual quality inspection systems. Complex implementation and calibration efforts consumed valuable time and energy when implementing vision jobs for new product variants. False negatives – and thereby time wasted on troubleshooting defects that in fact were not there – were unavoidable, because images of all possible defect types were not available. Consequently, the conventional visual inspection systems used at Siemens Rastatt slowed down their test engineers; a no-go in a “high-mix, high-volume” factory.
Alexander Dierolf
Head of Data Value Center at Siemens Smart Infrastructure
Alexander Dierolf, Head of Data Value Center at Siemens Smart Infrastructure, identified the EthonAI Inspector software as a potential solution to the scalability problems in Siemens Rastatt’s visual inspection systems. EthonAI’s ease of use, rapid time-to-value, and low maintenance efforts met all critical needs of the company’s test engineers.
The EthonAI Inspector software ticked all the boxes for a usable, scalable, and actionable visual quality inspection system that boosts productivity. Additionally, the software allows for easy quality monitoring across multiple inspection stations, which increases the transparency of potential quality issues.
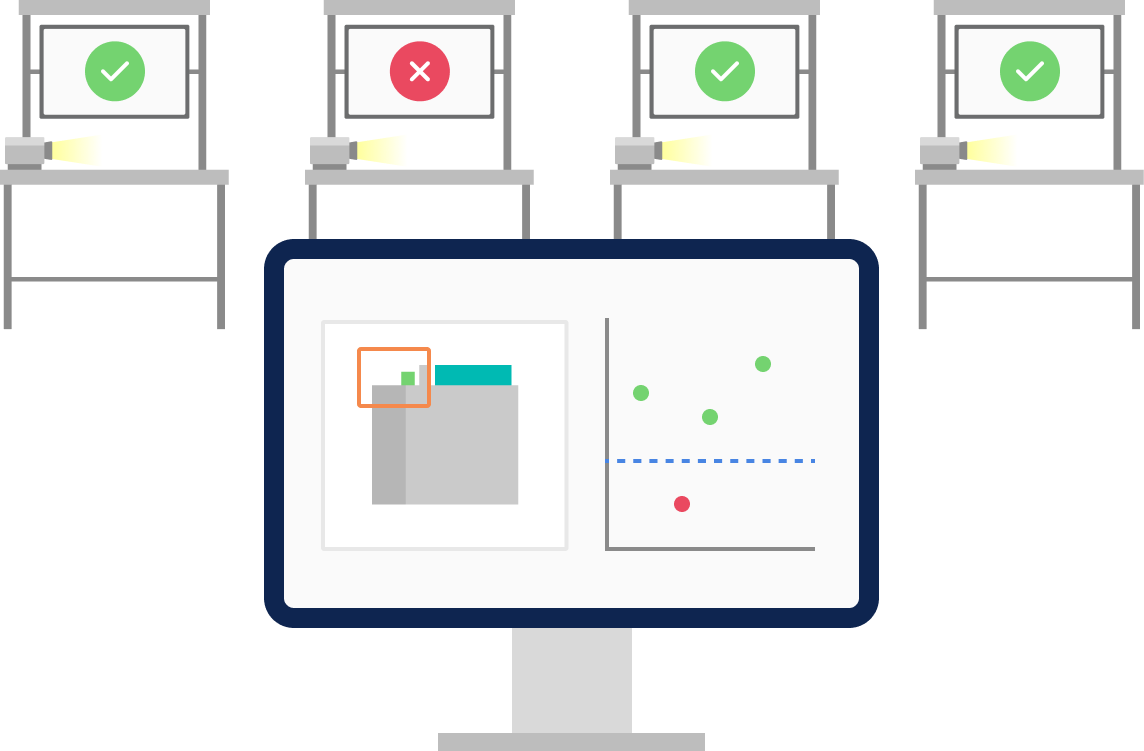
Daniel Krauth
Test Engineer at Siemens Rastatt
What started as a benchmarking of the EthonAI software in mid-2022 has developed into a long-term collaboration across multiple Siemens factories. Engineers use the EthonAI Inspector to create and assess visual inspection jobs faster than ever. “Thanks to the EthonAI Inspector software, new product variants can be integrated within minutes,” explains Daniel Krauth, Test Engineer at Siemens Rastatt. He adds, “It also enables us to detect unexpected defects before they reach our customers.”
By March 2023, Rastatt test engineers had performed over 150’000 inspections across 200 product variants with the EthonAI Inspector software, achieving perfect defect detection. By identifying defects earlier in the production process, they are now preventing defective products being shipped to customers and have relieved concerns about unexpected defects going unnoticed. “We are a convinced customer!”, Alexander Dierolf exclaims. “We are currently rolling out EthonAI across our factories in Europe and the US.”
Impact
Minimal inspection setup in high-mix production
Perfect Detection
The EthonAI Inspector found 100% of defects. Even unexpected ones, because the system does not need examples of possible failure cases.
Fast Setup
With 200 product variants, setup times for inspection jobs become crucial. With the Inspector, setup now takes the Test Engineers minutes instead of days.
Workforce Support
Troubleshooting false-negatives is wasteful. Our tool shows defect heatmaps to workers, enabling them to make better judgment calls faster.